With HORUS, MetGauge provides a cost-efficient stationary optical measuring system for continuously testing the dimensional accuracy of coldly formed, thermally treated or hot rolled products of a cross-sectional size up to 300 mm (12 inch). The measurement range is up to 330 mm (13 inch). However, pass-line variations have to be considered. Diameter and roundness, width, height and other measurements on convex shapes (rounds, flats, squares, hexagonal) including reinforced bars with rib structures and L-shaped angles are performed online, results displayed and alarms set, in case the product exceeds its pre-defined tolerances. Product measurements from earlier productions can be accessed through an integrated database for a seamless documentation of product quality.
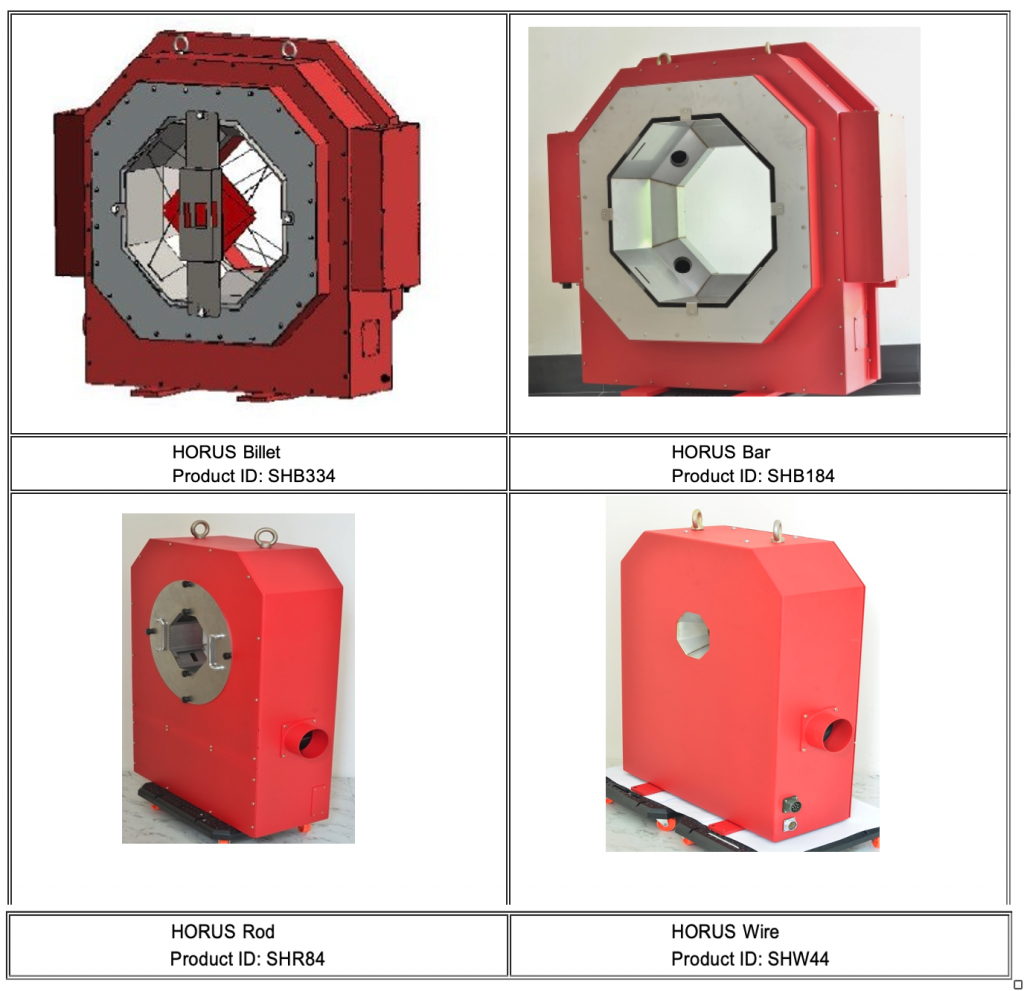
HORUS Wire can be applied to material temperatures of up to 1200°C (or 2200°F) and ambient temperatures between -10 – 50°C (14 – 122 °F). The integrated cooling/heating system keeps the sensor temperature constant, while very hot material runs through the gauge close to the sensors. Thanks to this early quality control, steel mills can find root causes for defects and implement suitable corrective measures much earlier, reducing their reject rate and associated cost.
HORUS Wire is ready for the use in hot rolling mills, wire or bar mills. The measurement area is a closed ring, allowing to move the gauge out of the line between 2 billets. One data set is collected over one billet and stored in the data base for later retrieval.
Measurements are carried out on a variety of features depending on the cross-section shape or contour of the product. The values are taken 1000 times per second and are compared against the allowed tolerances. The amount of raw data acquired by the sensors is quite big and would fill any reasonable size of mass storage within a short time. Therefore, an advanced filtering of these data is executed.
If the tolerance limit is exceeded, an alarm is generated and the complete contour is stored for further retrieval and analysis, otherwise a regular contour sample is taken, adjustable e.g., every 0.1 s, and stored. For special evaluations selected values, e.g., diameter or height and width, can be stored more often, adjustable up to for every scan, that means 1000 times per second.
For round material, the diameter measurement is essential. HORUS Wire calculates the smallest and the biggest diameter, average and standard deviation as well as the roundness. Also, the angle, under which the smallest and the biggest diameter has been measured, can be calculated. Additionally, the cross-section area is evaluated for every scan, while the meter weight is calculated from the average cross-section area over a reference length (adjustable, usually 1 m).
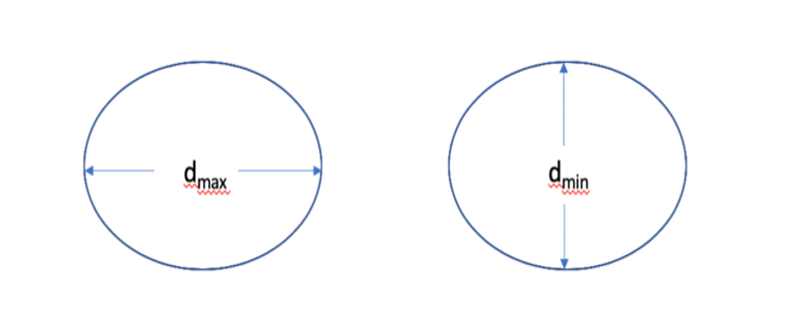
HORUS Wire measures the following features for rectangular shapes like squares and flats:
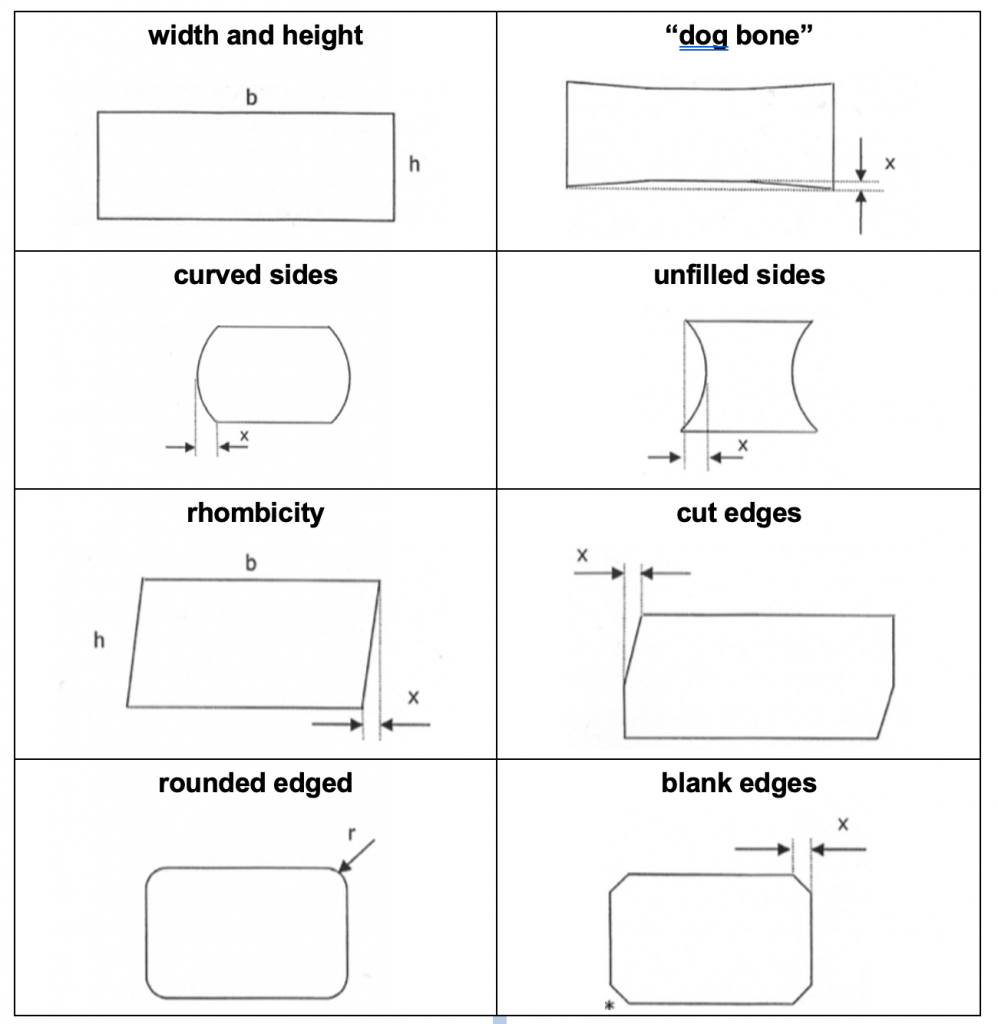
Examples of typical and recognizable rolling defects are:
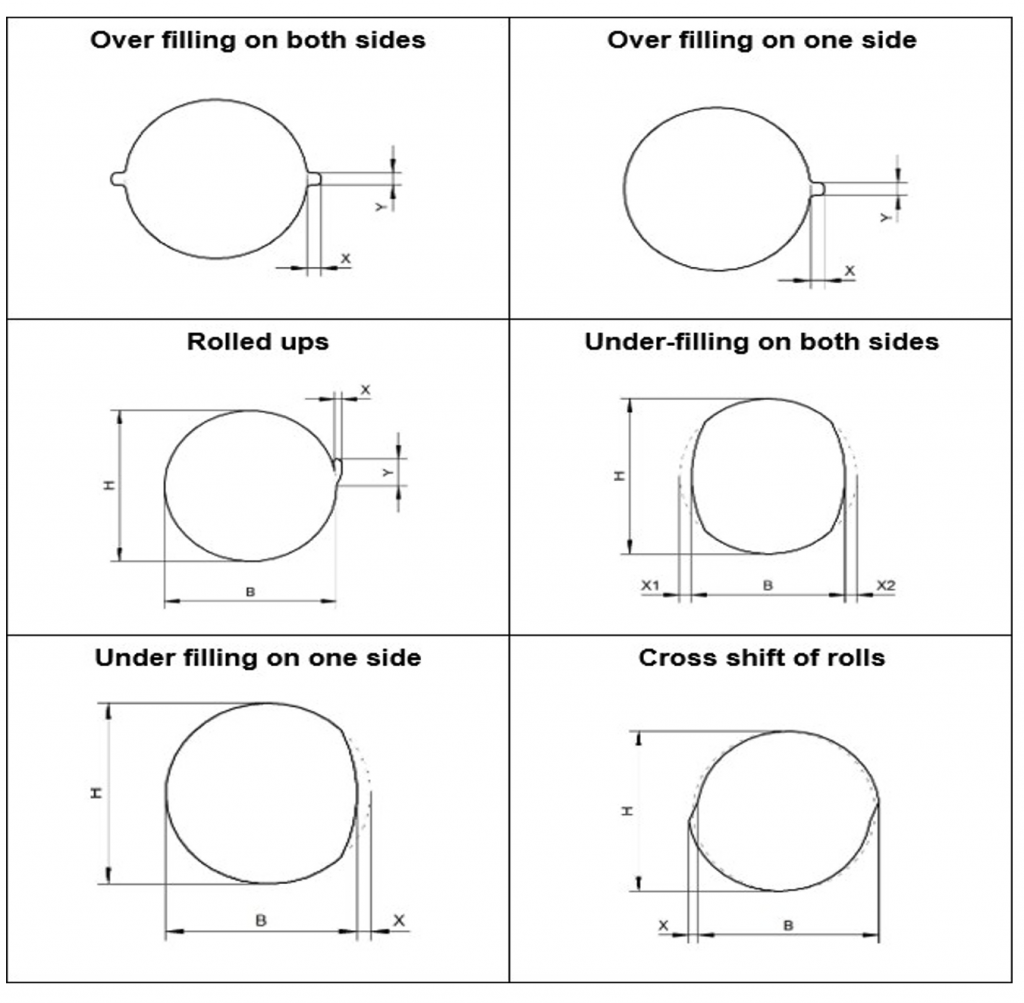
The measurement area is a closed ring, allowing to move the gauge out of the line between 2 billets. One data set iscollected over one billet and stored in the data base for later retrieval.
Measurements are carried out on a variety of features depending on the cross-section shape or contour of the product. The values are taken 1000 times per second and are compared against the allowed tolerances. The amount of raw data acquired by the sensors is quite big and would fill any reasonable size of mass storage within ashort time. Therefore, an advanced filtering of these data is executed.
If the tolerance limit is exceeded, an alarm is generated and the complete contour is stored for further retrievaland analysis, otherwise a regular contour sample is taken, adjustable e.g., every 0.1 s, and stored. For specialevaluations selected values, e.g., diameter or height and width, can be stored more often, adjustable up to for every scan, that means 1000 times per second.
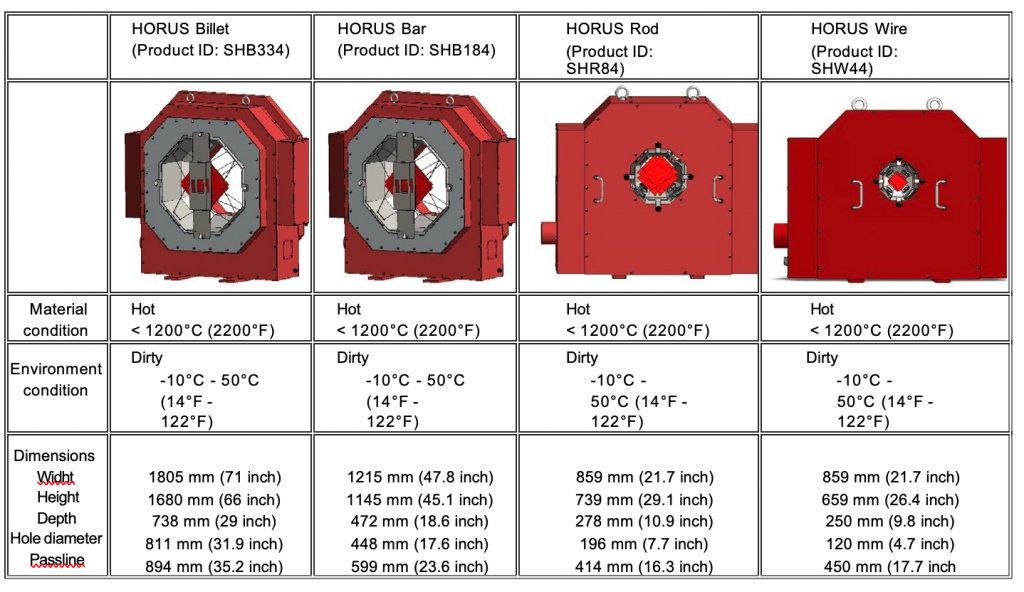